CURRENT STATUS
Introduction to B12 Petroleum Company
Introduction to B12 Petroleum Company
B12 Petroleum Company, from a bird's-eye view B12 Petroleum Company (B12) originated from the Quang Ninh Petroleum Reception Company. Its petroleum infrastructure includes reception ports, storage tanks, and the first petroleum pipeline system built with assistance from the former Soviet Union. The construction of the system was designed and executed from 1969 and was completed by June 1973, aiming to supply and ensure fuel sources for the southern battlefield during the resistance war against the United States for national salvation.
As the leading unit of the Vietnam Petroleum Corporation in the northern region, B12 Petroleum Company manages and operates various facilities, including a petroleum reception port capable of receiving vessels up to 40,000 DWT, five petroleum storage warehouses with a total capacity of 337,200 m3, an interconnected pipeline network spanning nearly 600km, passing through six provinces and cities: Quang Ninh, Hai Phong, Hai Duong, Hung Yen, Bac Ninh, and Hanoi. Additionally, it operates 118 petroleum retail stations.
At the main port, it currently receives over 4 million m3 of various types of petroleum annually, which is pumped through pipelines to the Duc Giang Warehouse in Hanoi, the Thuong Ly Warehouse in Hai Phong, and the K135 Petroleum Warehouse in Phu Ly, Ha Nam.
The company's main tasks include ensuring the fuel supply for economic and social development, ensuring national energy security for most coastal provinces, the Red River Delta, and the northern mountainous region. It also engages in petroleum and petroleum product trading, meeting the demands for socio-economic development and ensuring the national defense and security in Quang Ninh, Hai Phong, Hai Duong, and Hung Yen provinces. Additionally, it participates in the national petroleum reserve plan.
Current Status before implementing the project at B12.
Regarding procedures and regulations:
For each specific type of machinery and equipment, B12 has specific procedures and regulations governing maintenance and periodic repairs at different levels. However, currently, the work is not specifically differentiated according to the procedures. Specifically, each year, the unit plans general maintenance and repair schedules for each type of equipment. When it is time for maintenance and repair, the assigned technical staff will carry out the tasks based on the specific condition of each type of equipment. The levels include maintenance, replacement repair, major overhaul, medium overhaul, minor overhaul, inspection, calibration, etc.
Regarding equipment record management:
Currently, the updating of records and other information is only tracked for some machinery and equipment in the main production line (tanks, transformers, main pumps, vessels, etc.). Equipment that is not included in the record updates is directly assigned to personnel responsible for direct monitoring and information updates. As a result, the tracking and information updates for these devices are not comprehensive and accurate, posing difficulties in management tasks.
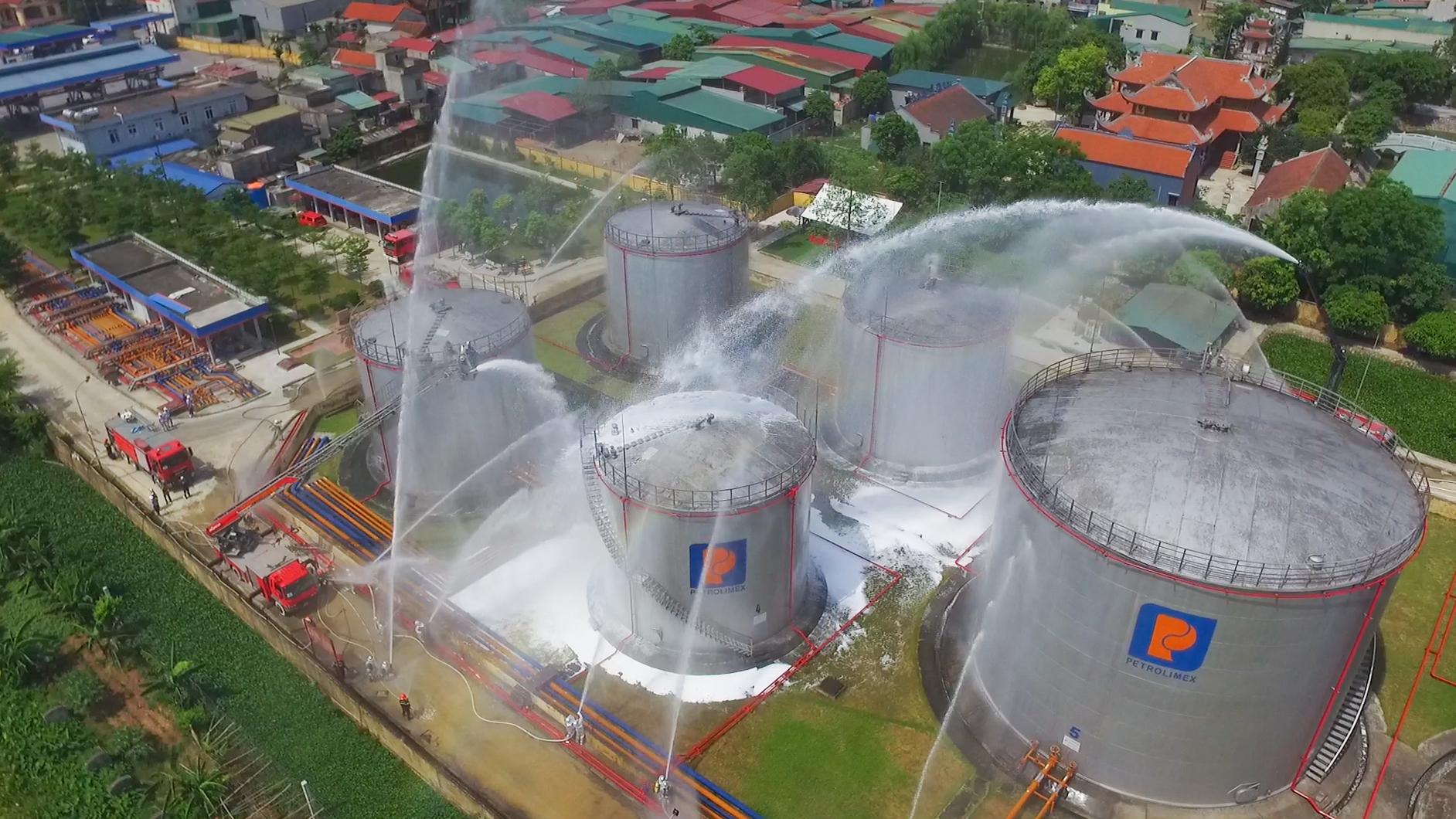
Regarding the storage tank system with a large scale at B12
Regarding the storage tank system with a large scale at B12:
In terms of repair and maintenance work:
The management work currently does not have a systematic approach to handling unscheduled/periodic repair and maintenance of equipment. As a result, the company's leadership/Technical Department faces difficulties in monitoring, planning, and executing equipment repair and maintenance.
Regarding reporting:
- Periodically, units at B12 will generate reports based on existing regulations, such as:
- Comprehensive report on the status of technical equipment (Quarterly)
- Report on the performance status of good shift stations (Quarterly)
- Report on pipeline operation mode (Quarterly)
- Record of periodic inspection of pipeline thickness (Annually)
- Future capability prediction
- Protocol for periodic inspection of lightning protection and static electricity systems (Annually)
The data for these reports are derived from statistical records and technical documents, requiring considerable effort and time to complete the reports.
Regarding supporting tools:
In 2012, Petrolimex implemented the SAP software. SAP is an Enterprise Resource Planning (ERP) software solution that encompasses specialized functions for managing various business activities, ranging from upstream supply chain management, oil refining, asset management, to administrative and support functions such as finance, human resources, analysis, control, etc.
B12 utilizes the asset management subsystem of the SAP software to manage information about assets and tools at the company. However, B12 primarily utilizes this software from an accounting perspective, focusing on information such as original cost, depreciation, etc. Information related to technical specifications, maintenance, and both scheduled and unscheduled repairs are not yet managed within the SAP software. Overcoming this challenge and enhancing monitoring and control tasks is one of the goals that B12 aims to achieve.
DEPLOYMENT SCOPE
Deployment Objectives
Based on HPT's deployment experiences, combined with management requirements, the project team has defined the following specific objectives:
- Manage the entire documentation and lifecycle of equipment and technical infrastructure invested in Company B12.
- Monitor the operational status of equipment in the production line closely.
- Support planning, monitoring, and supervision of inspection, maintenance, repair, testing, calibration, and equipment validation according to relevant standards/regulations/norms.
- Minimize omissions, reduce the need for additional technical plans, and decrease the preparation time for maintenance and repairs.
- Predict future capabilities and responsiveness.
- Enhance the effectiveness of overall operations, retrieval, and search of technical infrastructure from the Company to the respective units.
With clear objectives like the above, HPT has proposed the deployment in specific phases as follows:
Main Deployment Phases at B12
Deployment Activities
Understanding the management objectives of B12 Petroleum Company quickly, HPT collaborated with the B12 Project Board to implement the following work items:
1. Classify all types of assets and tools across the entire scope of B12 Company to establish uniformity in identification and classification during the data entry process for technical infrastructure, as well as future operation and exploitation.
2. Build a database and data entry templates for technical infrastructure information. Provide centralized training and instructions to all units to avoid errors in data entry in the future.
3. Configure and customize the software with features that meet the management objectives of B12 Petroleum Company, including:
a. Manage information according to the lifecycle of technical infrastructure: from the asset phase, equipment being put into use, going through usage stages, status changes, information updates, transfers, etc., until the asset or equipment is disposed of or liquidated.
b. Plan and report on maintenance, repair, inspection, and calibration activities based on criteria such as regular and ad-hoc schedules.
c. Automatically send notifications and alerts to technical personnel and management staff to prevent any omissions regarding different types of assets and equipment.
d. Advanced search and filtering capabilities with over 20 criteria.
e. Diverse reporting system with important criteria to support quick and convenient management reports, such as inventory reports, status reports, planning reports, maintenance/repair results reports, etc.
4. Provide guidance and training on how to operate and utilize the software for all units of B12 Petroleum Company. Empower operational teams, including technical and management personnel, to fully grasp the software's functionalities.
ACHIEVED RESULTS
After 3 months, HPT successfully collaborated with the B12 Project Board to deploy the project, achieving the following specific results:
- Established regulations for managing the technical infrastructure of B12 Petroleum Company applicable to all units, ensuring control over the management, monitoring, and utilization of assets and equipment at B12.
- Additionally, B12 Company was provided with software equipped with excellent features to support the management of technical infrastructure, including:
a. Category management and system administration: User account synchronization with the Group's Active Directory (AD). User administration setup based on requirements.
b. Profile and lifecycle management of technical infrastructure, displaying necessary information for each device, device type, equipment group, or any relevant information regarding technical equipment. The software also allows for establishing parent-child relationships between equipment, making management and monitoring tasks easier.
c. Maintenance, repair, inspection, and calibration management feature for assets and technical equipment, including planning and providing automatic alert mechanisms and reminders for regular activities.
d. Information search: The software enables users to quickly search and analyze one or multiple types of assets and technical equipment with over 20 different filtering options, based on various groups. It offers ease of use and flexibility in management tasks.
e. Reports: The system currently provides 18 reports, including important ones such as:
+ Asset and tool inventory reports according to accounting standards.
+ Planned maintenance, repair, inspection, and calibration reports for technical equipment and tools based on regular/ad-hoc schedules or operational specifications.
+ Results reports for maintenance, repair, inspection, and calibration activities for technical equipment and tools based on regular/ad-hoc schedules or operational specifications.
+ Detailed profiles of assets, technical equipment, and tools based on different selected criteria.
+ Reports on asset disposal and status of technical equipment.